Understanding the Role of an Operations Manager in Leadership
An organization’s daily operations function successfully because operations managers ensure all production functions match company goals, logistics, and team performance. These professionals focus on rearranging processes for better efficiency alongside eliminating operational inefficiencies to uphold departmental operational coherence. As leaders of operations, managers need to make timely decisions while supervising staff in numerous locations and handling urgent responsibilities. Their leadership performance determines how employees work, how safe the workplace stays, and what operational goals can be reached.
Operations managers need to guarantee clear communication while maintaining consistent oversight and robust safety protocols since they oversee personnel who work in different locations, such as warehouses and facilities, alongside
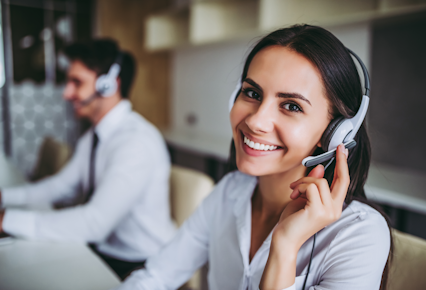
remote field environments. The team leader must handle the responsibilities of shift scheduling and equipment maintenance, together with enforcing protocol compliance for every team member. Operations managers take ultimate responsibility for worker safety within dangerous positions that exist separately from main facilities. Leadership in this situation demands specific approaches that maintain operational effectiveness and safeguard protocols.
Operations managers who demonstrate strength create risk anticipations, which lead to preventative measures against outbreaks of potential disruptions. The creation of backup plans alongside quick issue resolutions and operational link cohesion are duties assigned to these professionals. The organization must provide all personnel, but especially those working without partners, with suitable equipment and assistance. Their leadership style derives from existing situation understanding, together with safety-centered planning and accountability. Lone workers benefit from specific systems that enable them to seek quick help, which reduces operational downtime and minimizes their risk exposure. Operation leadership involves both task management and direct protection of personnel who execute their responsibilities.
How Lone Worker Solutions and Alert Devices Help Operations Managers Improve Employee Oversight and Safety
Operations managers must continuously address the management of workers who operate in remote locations. Lone worker solutions, which consist of GPS-enabled tracking devices as well as automatic check-in systems and emergency alert tools, create a systematic method for operations managers to remotely oversee their staff. Lone worker devices report employees' current status and position in real-time, which gives managers instant information to support quick decision-making processes. Standard operating procedures that include such technological tools enable managers to observe operations while their employees operate from locations without direct contact.
The systems deliver maximum value for environments where workers perform alone because they need protection from dangerous situations and operational hazards. Lone workers have access to alert devices that enable them to start an immediate emergency signal when they face medical or injury conditions or dangerous situations. Operations managers receive instant notifications, which enables them to deploy help services promptly and execute quick assistance decisions. The early warning capability enables operations managers to reduce injuries as well as minimize operational waits and meet their responsibilities for safeguarding workers at risk.
The collection of safety data by operations managers through lone worker technologies enables the assessment of safety patterns while providing insights about response times, along with areas that require training or support enhancement. Accumulated data through time enables better organizational decision-making, which leads to improved safety protocol development. Managers achieve better safety standards by identifying specific locations with high risk frequency and roles that face the highest vulnerability. Lone worker devices assume strategic leadership functions by integrating protection measures into every operational workflow.
Why Lone Worker Policies Matter for Operational Safety and Compliance?
Safety policies form a main operational responsibility for managers to implement and enforce in every workplace environment. Lone workers risk of emergencies because they work without immediate supervision in their conditions. An established lone worker policy gives employees both guidance about emergency protocols and protective framework systems when incidents occur. Operations managers are responsible for implementing these policies both to fulfill regulatory requirements and to maintain general safety rules throughout all parts of their business. This includes consistent monitoring, clear enforcement, and internal audits to ensure accountability. Compliance-driven safety protocols allow for real-time updates, hazard identification, and streamlined reporting procedures. These efforts improve risk mitigation and ensure support systems are accessible when most needed.
Various mandates in multiple jurisdictions obligate organizations to determine their lone workers, together with appropriate procedures for emergency identification and response. Operations managers implement and monitor safety policies for the entire workforce to accomplish regulatory requirements through their on-site coordination. Operations managers must verify that checking-in processes operate correctly, as well as confirm emergency contact details and validate the operation of alert systems. Operations managers achieve regulatory compliance through alert devices that provide them with assurance to deliver immediate assistance to lone workers at their respective locations.
The establishment of lone worker policies enables operations managers to build safety-focused working cultures within their workforce. The policies combine expected standards with superior communication tools to grant employees peace of mind about their protection during self-work hours. Operations managers create trust and accountability through daily practice that incorporates safety compliance standards throughout their entire workforce. Through their leadership, workers receive all necessary resources to deal with emergencies, together with constant oversight from their team. The organization achieves operational continuity through its approach that places workforce welfare at the forefront of its risk management methodology.
Final Thoughts
Operations managers possess the opportunity to enhance workplace efficiency and safety, specifically when it applies to lone worker situations. Lone worker safety practices improve when operations managers combine alert devices with well-defined safety protocols into their current work systems to enable better oversight and rapid emergency response capabilities. Through these tools, operations managers fulfill compliance requirements and provide active protection to their teams. Operational leadership focused on safety creates advantages for all parts of the organization, starting with lone workers and reaching up to the entire organization. The adoption of lone worker solutions creates operational areas that become more secure and increase both legal compliance and operational readiness. Lone worker solutions implemented by operations managers will cultivate safety-conscious operations, which decrease workplace incidents while strengthening staff loyalty. Through their leadership, employees gain confidence to work without fear because leadership ensures their well-being takes priority. Lone worker program implementation proves itself as a strategic investment for protecting employees while enhancing work productivity.